top of page

Homepage ❯ Composites ❯ Processes ❯ Closed Molding ❯ Here
Vacuum Infusion Processing
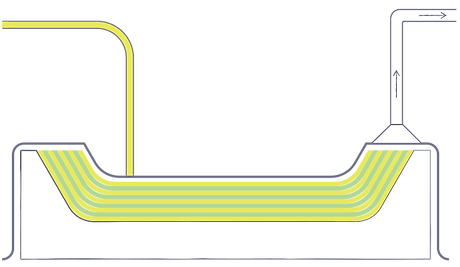
Vacuum infusion processing (VIP) is a technique that uses vacuum pressure to drive resin into a laminate. Vacuum infusion is typically used to manufacture very large structures. Vacuum infusion produces strong, lightweight laminates and offers substantial emissions reductions (compared to open-molding processing and wet lay-up vacuum bagging). This process uses the same low-cost tooling as open molding and requires minimal equipment.
VACUUM INFUSION PROCESSING is a variation of vacuum bagging in which the resin is introduced into the mold after the vacuum has pulled the bag down and compacted the laminate. Vacuum infusion can produce laminates with a uniform degree of consolidation, producing high strength, lightweight structures. This process uses the same low-cost tooling as open molding and requires minimal equipment. Vacuum infusion offers substantial emissions reduction compared to either open molding or wet lay-up vacuum bagging.
The method is defined as having lower than atmospheric pressure in the mold cavity. The reinforcement and core materials are laid-up dry in the mold by hand, providing the opportunity to precisely position the reinforcement. When the resin is pulled into the mold the laminate is already compacted; therefore, there is no room for excess resin. Vacuum infusion enables very high resin-to-glass ratios and the mechanical properties of the laminate are superior. Vacuum infusion is suitable to mold very large structures and is considered a low-volume molding process.
Process:
The mold may be gel coated in the traditional fashion. After the gel coat cures, the dry reinforcement is positioned in the mold. This includes all the plies of the laminate and core material if required. A perforated release film is placed over the dry reinforcement. Next a flow media consisting of a coarse mesh or a “crinkle” ply is positioned, and perforated tubing is positioned as a manifold to distribute resin across the laminate. The vacuum bag is then positioned and sealed at the mold perimeter. A tube is connected between the vacuum bag and the resin container. A vacuum is applied to consolidate the laminate and the resin is pulled into the mold.
Molds:
Molds are similar to those used for conventional open-mold processes.
bottom of page