top of page

Homepage ❯ Composites ❯ Processes ❯ Closed Molding ❯ Here
Pultrusion
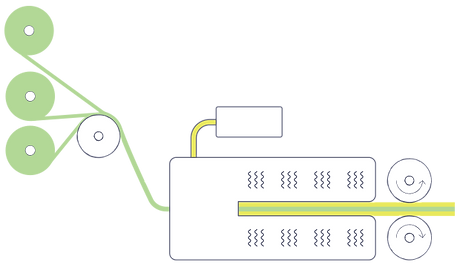
Pultrusion is used to form composites into long, consistent shapes like rods or bars. Continuous strands of reinforcement are pulled through a resin bath to saturate them, then pulled through heated steel molds that sculpt the composites into continuous lengths. The process operates continuously so it can be readily automated. Labor costs are low and finished products are very strong.
PULTRUSION is a continuous process for the manufacture of products having a constant cross section, such as rod stock, structural shapes, beams, channels, pipe, tubing, fishing rods, and golf club shafts. Pultrusion produces profiles with extremely high fiber loading; thus, pultruded products have high structural properties. The process can be readily automated and is adaptable to both simple and complex cross-sectional shapes. Very high strengths are possible and labor costs are low.
Process:
Continuous strand glass fiber, carbon fiber or basalt fiber roving, mat, cloth, or surfacing veil is impregnated in a resin bath and then pulled (therefore the term pul-trusion) through a steel die by a powerful tractor mechanism. The steel die consolidates the saturated reinforcement, sets the shape of the stock, and controls the fiber/resin ratio. The die is heated to rapidly cure the resin. Many creels (balls) of roving are positioned on a rack, and a complex series of tensioning devices and roving guides direct the roving into the die.
Molds:
Hardened steel dies are machined and include a preform area to do the initial shaping of the resin-saturated roving. The dies include heating which can be electric or hot oil. The latest pultrusion technology uses direct injection dies, in which the resin is introduced inside the die, rather than through an external resin bath.
bottom of page